3D printed medical devices, houses, and cars are now a reality.
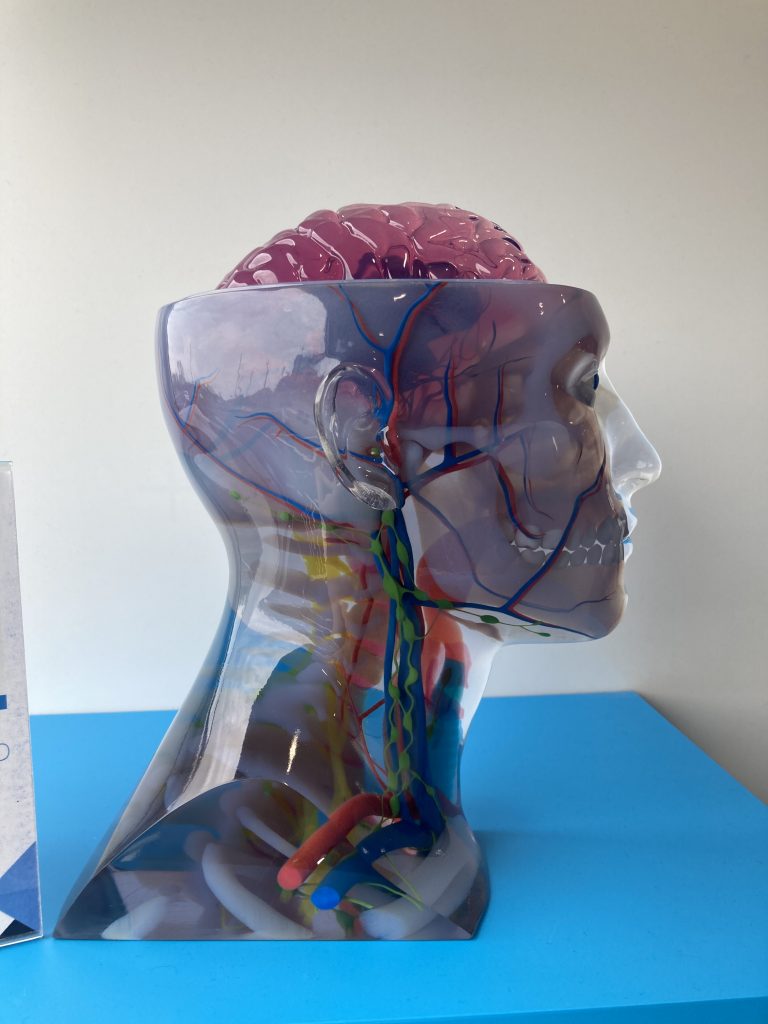
Over the summer I attended a product demonstration hosted by Stratasys (not affiliated). As someone that manages a Makerspace where students learn about and practice 3D printing, I am always interested in the latest technological innovations. Even if I can’t incorporate them into my lab now, I can pass that knowledge onto students and think about what will help our students prepare for the future as they choose an industry to pursue, or as we decide to incorporate more tech down the line.
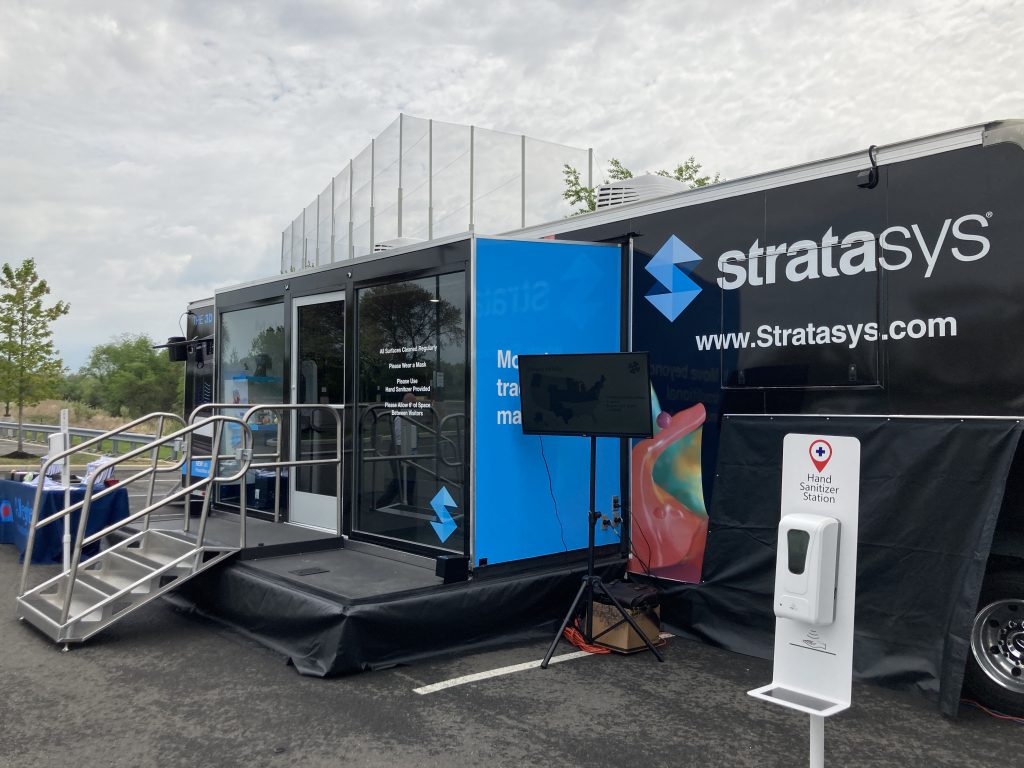
The representative from Stratasys welcomed me on their tour bus, which housed some of their most recent models for 3D printing. One had a large-scale chamber that could be used to print usable parts out of tough thermoplastics for things like refrigerators, while another had an impressive range of colors and textures it could produce in one print. By contrast, the printers in our lab can print a maximum of two colors (though we typically use the second option for support material rather than a color). Most hobbyist printers can only do one color at a time. In addition to color, the materials ranged from rigid plastic to somewhat flexible, rubbery material.
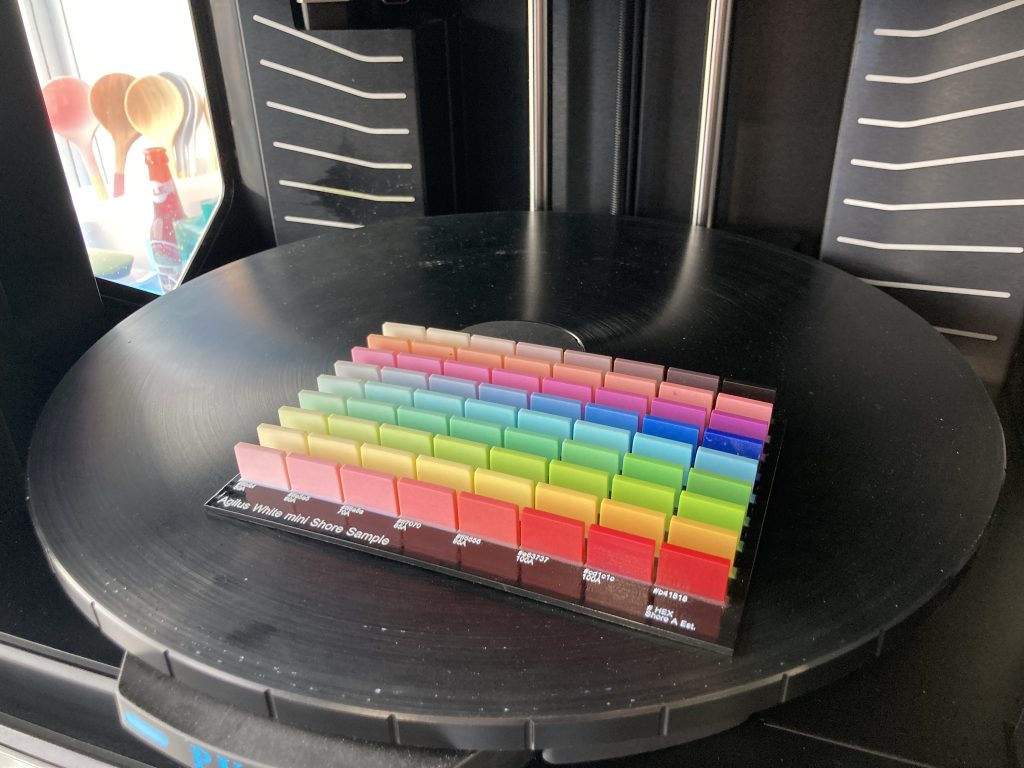
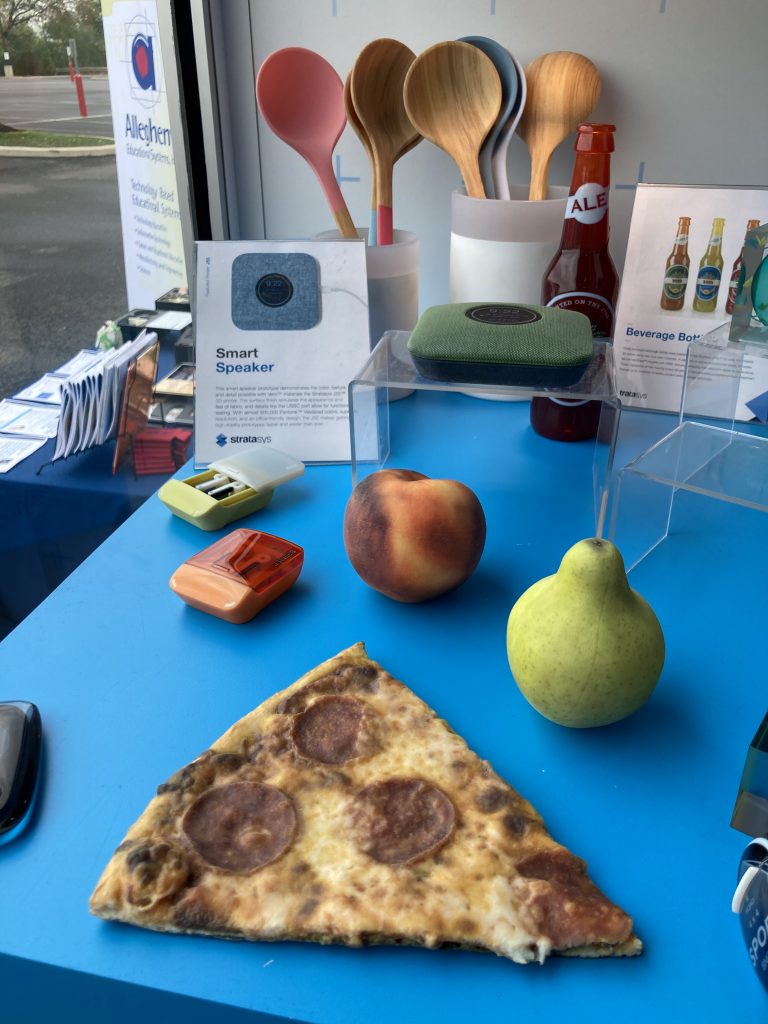
I was not expecting to see photo realistic 3D print samples of food like a slice of pizza, peach or pear. The difference in texture of the fruit skin was almost undetectable from the real thing, and the slice of pizza could easily have been picked up by someone at a party to take a bite. Fortunately the hardness of the pizza slice would deter anyone from breaking a tooth.
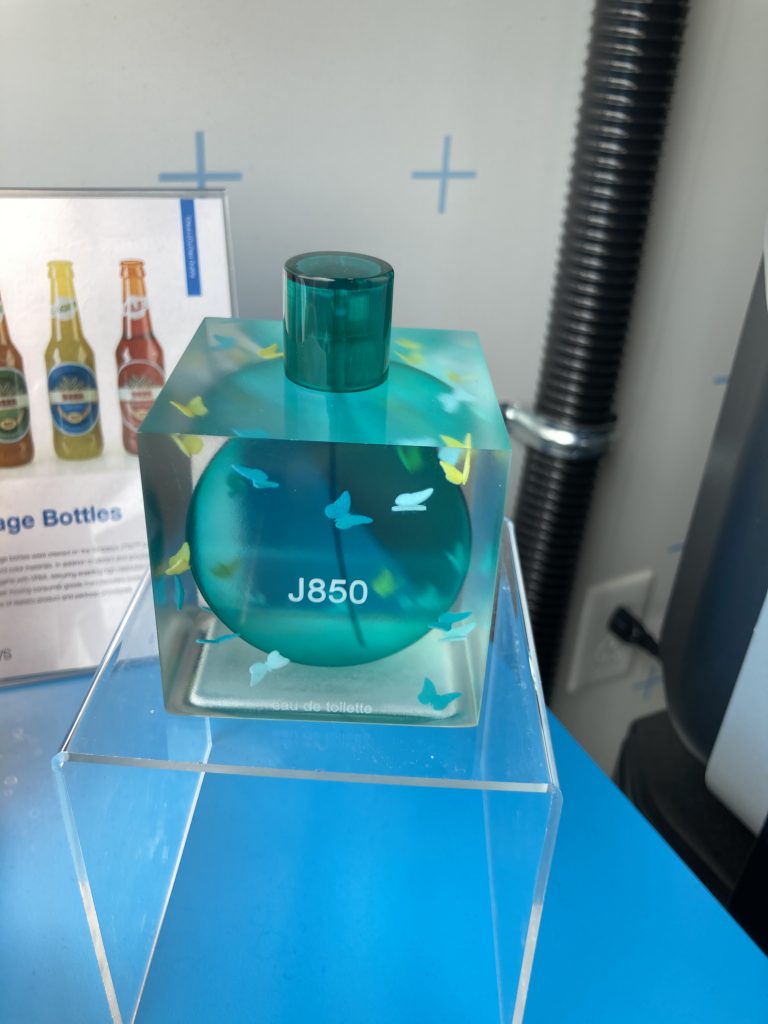
The implications for product design are mind blowing. This perfume bottle was 3D printed with multiple translucent colors, decorative butterflies that appear to be fluttering around inside of the cube, and text on the front of the bottle, which had the look and feel of glass (most likely some type of resin). This means that instead of sending designs to a manufacturer, which has to create the product using multiple processes such as mold making, casting, applying the text using a separate laser engraver, vinyl cutter, or ink printing process, the entire product can be designed, sent to the machine, and in hand within hours.
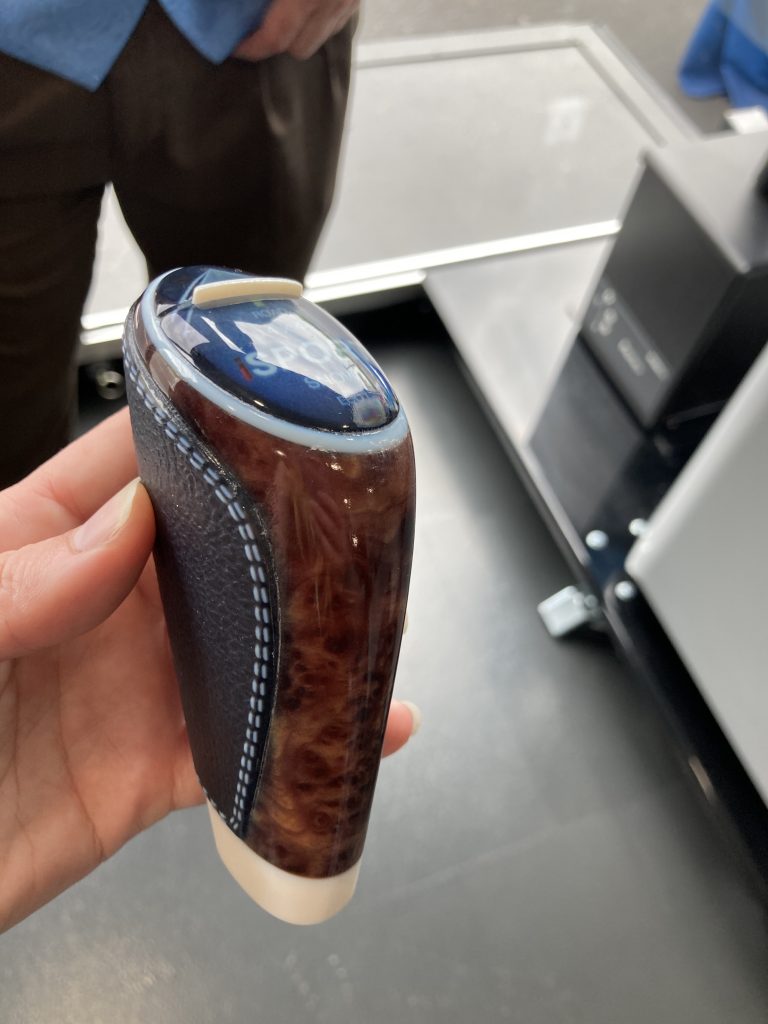
This 3D printed joystick was printed with all textures and colors as one piece. No post production assembly was required.
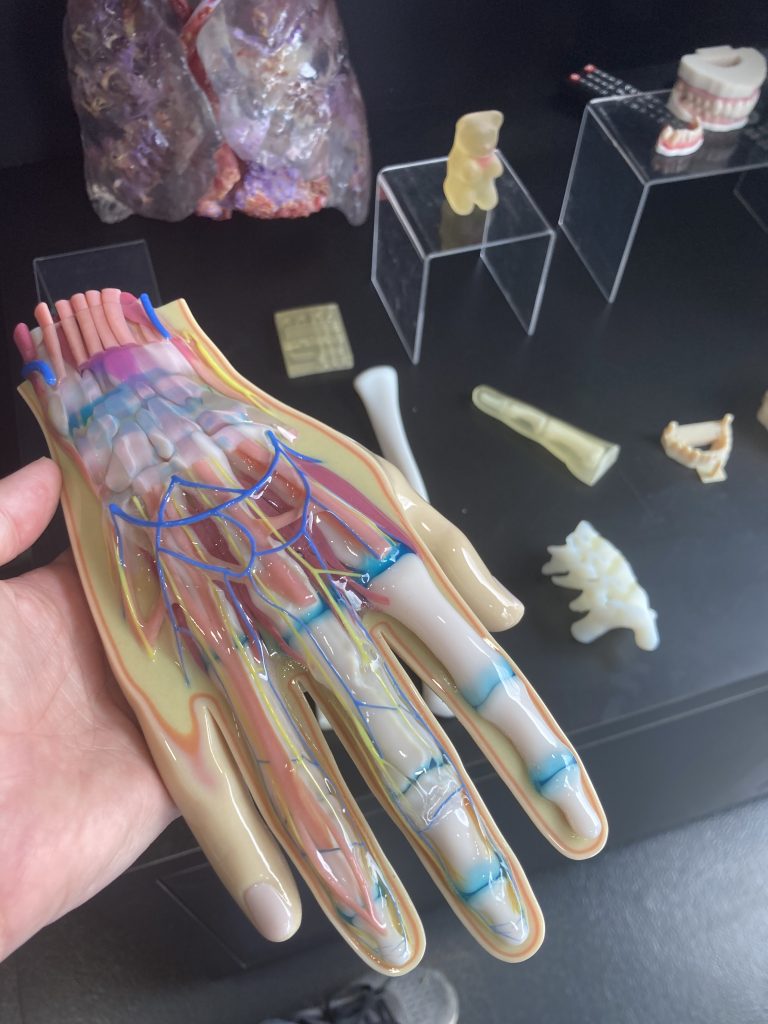
3D printing makes it possible to print accurate anatomical models from scans of real people, like aneurysms, so that medical students can better understand how to treat patients and researchers can make improvements in medical technology.

The additive manufacturing realm has added metal to the range of materials that can be 3D printed. The most common methods are either FDM (Fused Filament Fabrication, aka FFF), or DMLS (Direct Metal Laser Sintering). The first extrudes a filament that is comprised of metal particles and a plastic binder. After the print is complete, the part is thermo-treated to burn out the binder and anneal the part (shrinkage has to be taken into account when printing). The second uses a laser to fuse metal powder together in layers until the print is complete. Excess powder is removed and post processing thermal annealing helps with strength and accuracy. Manufacturers are now using 3D printing for car, airplane, and rocket parts.
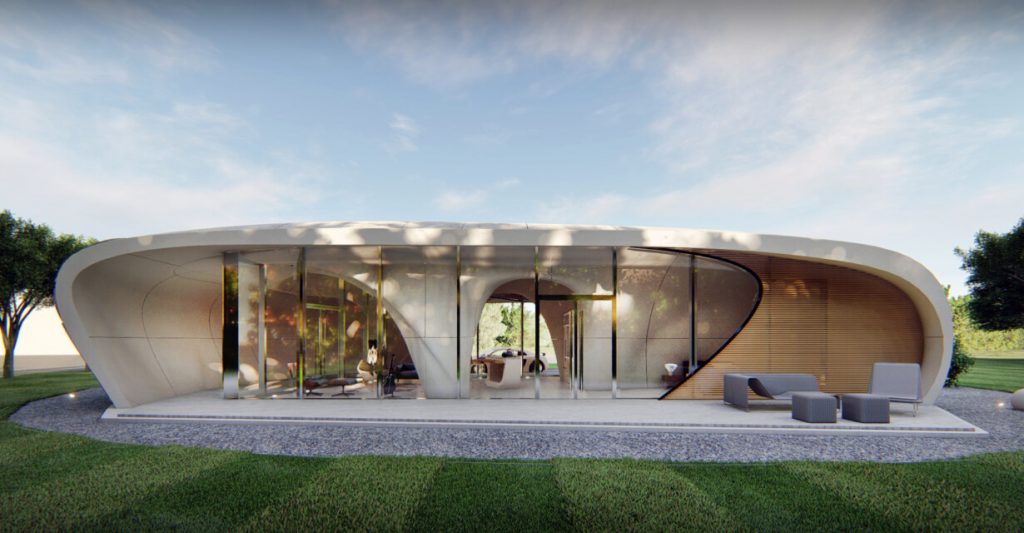
Great strides have been made in 3D printed architecture, which uses a similar method of extruding material in layers as the small scale 3D printers we have in our lab. Materials range from concrete to earthen mixtures, including hemp, expanding the range of forms that are possible. Check out this list of 3D printed houses. These methods can be used to build lower cost structures where they are needed most, like this entire campus of schools proposed to be printed in Fianarantsoa off the coast of Africa.
Additive manufacturing continues to expand the range of possibilities, making 3D printing cheaper, more accessible, and applicable to a wider range of practical uses. I am excited to see where the industry can take humanity as we pursue further innovation.
For information about the Makerspace at Swarthmore College, visit our website.