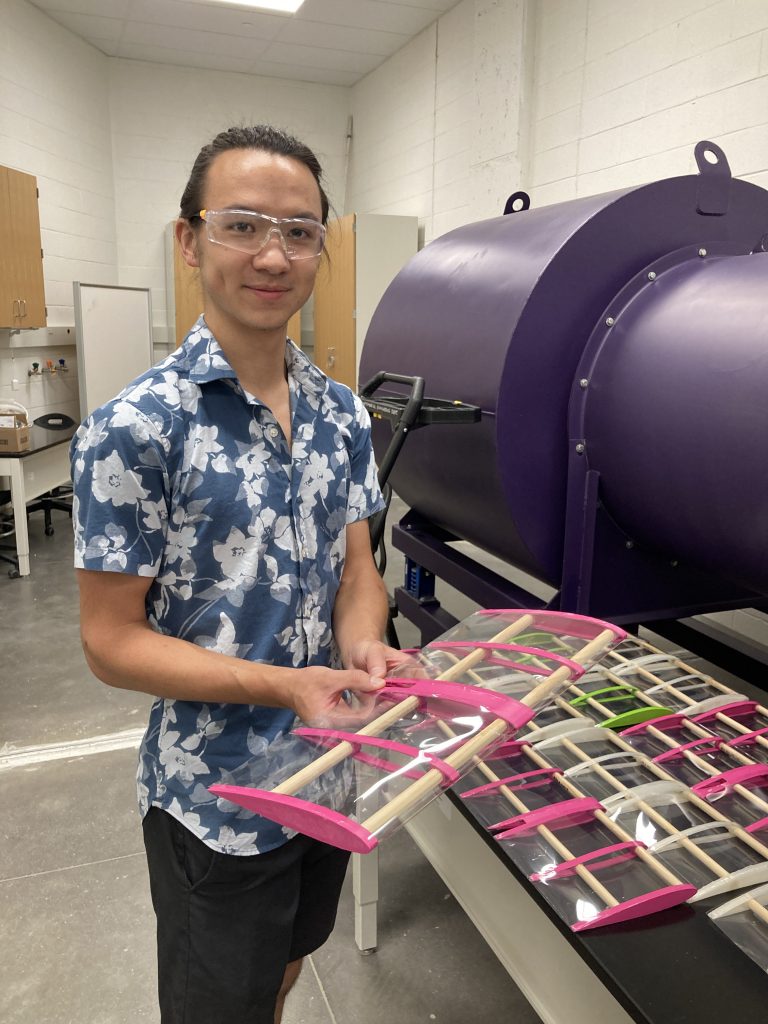
There are no shortage of strategies that people worldwide are using to find ways of generating sustainable energy. At Swarthmore College, Research Fellow, Joshua Vandervelde, class of 2023, has been working on a kite design for capturing wind energy, using a combination of our Makerspace 3D printers and the Engineering Department’s robust wind tunnel. Josh describes the benefits and challenges with this research.
1. What are energy kites and how do they work?
Generally, Airborne Wind Energy (AWE) kites are tethered kites that convert the kinetic energy of moving air into useful electricity, similar to how wind turbines harvest wind energy. AWE systems are not new concepts— a number of companies over the last decade have attempted to design and construct these kinds of systems with power outputs comparable to modern wind turbines. However, none of them produced kites reliable or economic enough to truly compete in the existing energy market.
AWE kites come in a variety of shapes and sizes, each with their own wildly different method of extracting wind energy, so I’ll only explain how I intend my kites to function. My kite—more easily thought about as a large wing—produces lift from the wind flowing across it. This lift causes the kite to move upward, but because a tether connects it to a spool anchored to the ground, it also unwinds the spool. The rotation of this spool causes an attached generator to spin, creating electricity. So the farther and faster the kite moves from the wind billowing around it, the more energy is harvested. Now at the top of this ascension, my kite does something rather unconventional: it inverts its shape, creating a new wing profile that creates lift in the downward direction. The wind blows the kite back toward the ground while the generator uses minimal energy to rewind its spool, and thus a net positive energy cycle is formed.
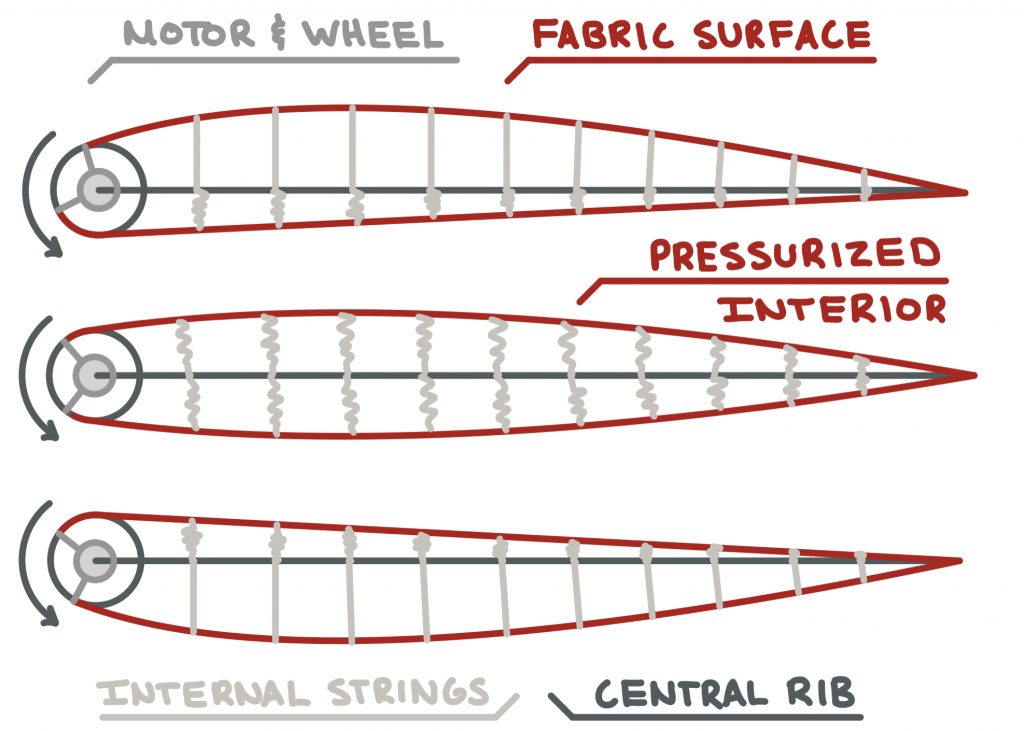
2. What are the roadblocks to using kites for kinetic energy?
Where shall I begin… if you’ve ever flown a kite on a windy day, you may remember the kite behaving rather erratically, shifting from side to side in fast, unpredictable swoops. Now imagine that same kite scaled in size about a hundred-fold, flown a thousand feet off the ground, and (periodically) racing back toward the ground faster than a dropped object of equal mass. AWE kites are frightening to think about from a system controls perspective, to say the least. For these kites ever to make it into the mainstream energy market, they have to be reliable, and that means creating an aerodynamic body with enough strength and stability to deal with high altitude wind streams but with as little mass as possible. And beyond all the onboard electronics and mechanisms to reasonably invert a kite’s shape, the grounded generator has to be beefy enough to deal with loads of thousands of pounds of force during ascension, then use hundreds more to reel the tether back in at the same rate that the kite descends. The entire system—spanning thousands of feet—has to work in unison, but simultaneously deal with potentially unpredictable winds.
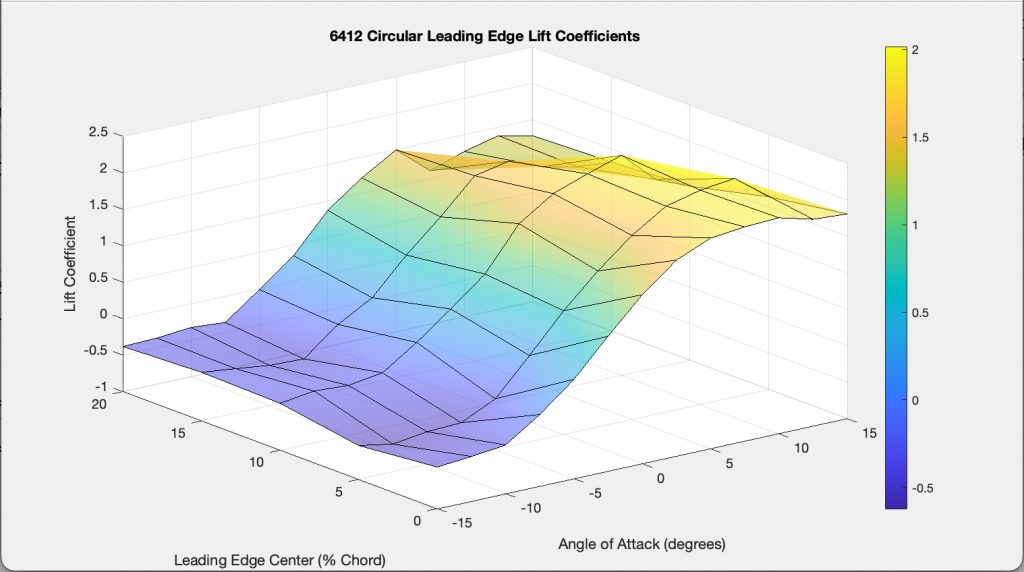
3. What then are the advantages of these kites over other wind energy alternatives?
If all stability and systems problems are figured out, AWE kites have the potential to produce wind energy at a fraction of the cost of wind turbines using a significantly smaller initial investment and with an added bonus of easy mobility. Wind velocities increase rapidly with altitude while becoming less turbulent, meaning that high altitude wind energy is simultaneously more consistent and more powerful than anything wind turbines will ever be able to tap into. AWE kites would only consist of airtight fabric, stiff rods for reinforcement, and the electronics and motors for inversion; they cost much less and are more easily constructed than multi-million dollar wind turbines. Finally, these kites lack the enormous concrete foundations necessary for turbines, meaning they can be deployed to remote communities, offshore wind farms, or even cargo ship decks (as SkySails has accomplished).
4. What are you trying to achieve with your kite design?
I’ve mentioned this concept of an “inverting kite” several times, but what truly distinguishes my AWE kite design from existing models is the kite’s ability to produce positive lift in one configuration and negative lift in another. The basic premise of this revolves around a circular leading edge that turns like a wheel to distribute the kite’s fabric surface to the top or bottom of the wing. The included diagram shows a side profile of the kite’s airfoil, where the turning leading edge pulls in fabric from the top of the kite and lets it bow out on the bottom. This action, paired with the kite’s interior pressure forcing the fabric to expand out, allows the kite profile to morph, creating negative or positive lift on command. This is what I refer to as inversion.
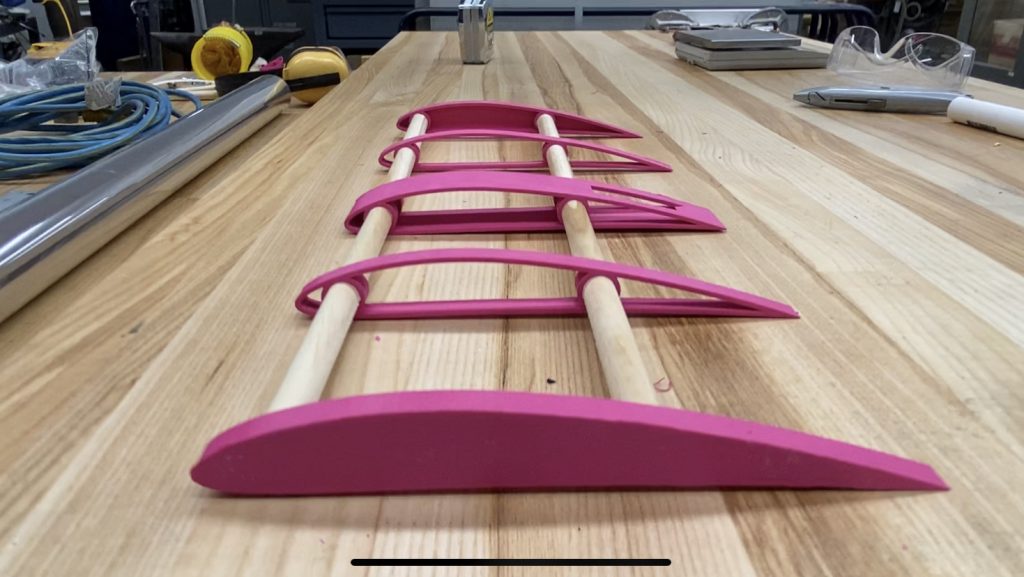
5. What software and equipment are you using to create your kite prototypes?
This past summer, I didn’t even get to prototyping the kite itself— to systematically determine the best kite shape for this kind of energy generation, I had to first start in two dimensions. No research has been conducted on airfoils with circular leading edges before, so to determine which lift and drag characteristics I would need for the kite—or even subsections of the kite, as wings are rarely continuous airfoils—I had to test a number of extended airfoils in the Swarthmore wind tunnel.
To fabricate these airfoils, I used MATLAB to generate the outlines of existing airfoils, specifically of the NACA series, and modified them to my desired specifications. With these spline outlines, I used Fusion 360 to create airfoil ribs, which I then 3D printed out in the Makerspace (in a variety of colors, I may add!), and finally assembled in the engineering machine shop. Lateral wooden dowels reinforced the airfoil ribs while a thin plastic layer sealed the ribs together. To test in the wind tunnel, I milled two aluminum support pieces compatible with the strain gauge so that I could accurately measure lift and drag of the airfoils. Finally, I conducted all tests and data analysis with MATLAB.
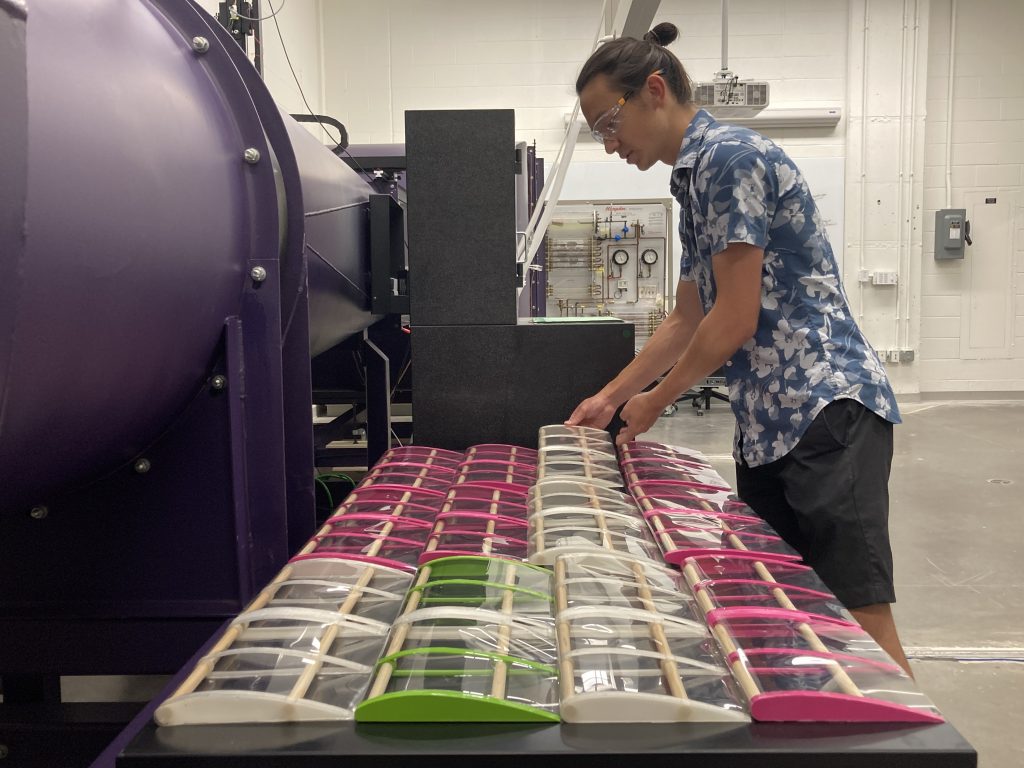
6. How many prototypes have you made?
I made thirteen airfoils in total, five of which are unmodified NACA models to compare to existing literature and while the other eight are modified versions with circular leading edges. I had already narrowed my search of reasonable airfoil shapes to use before fabrication (based on lift and drag coefficients, specifically at low angles of attack), so these thirteen models were likely all that I needed.
7. How do you test your prototypes?
Once constructed, I slid my airfoils vertically onto the stain gauge. Every airfoil was tested at angles of attack from -15º to 15º with 2.5º steps, and every angle of attack used three different velocities to average lift and drag coefficients. I then created data visualizations to compare the performances of modified airfoils, eventually deciding on a modified NACA 6412 airfoil with a circular leading edge 10% of the way along its unmodified chord, flown at an angle of attack of 5º to 10º as the optimal (initial) airfoil for my inverting kites.
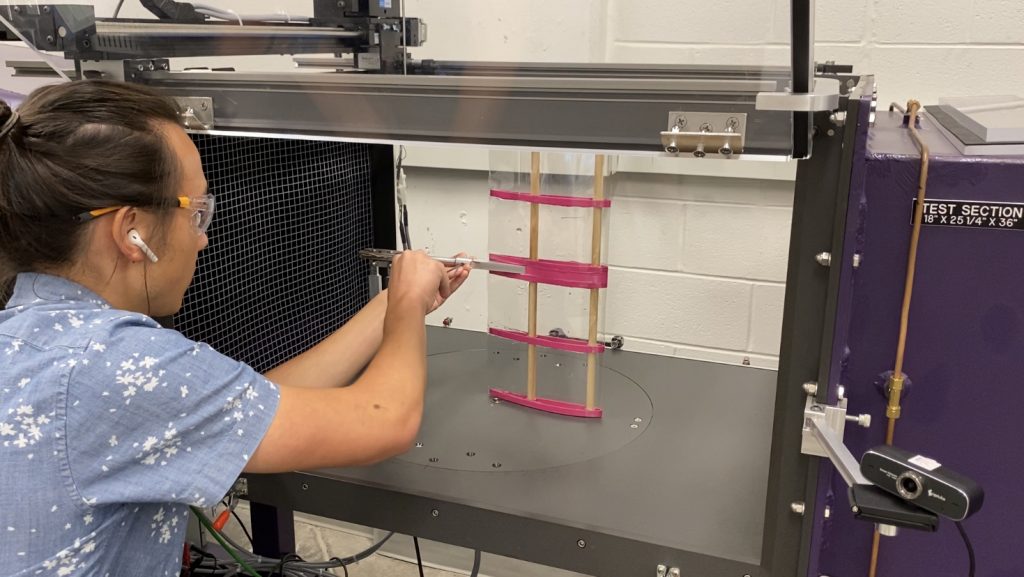
8. What would your ideal kinetic kite farm look like?
To be entirely honest, I doubt my AWE kites will ever fly on a commercial scale. I trust the theory behind these kites, and I recognize the advantages they propose, but years of work and the efforts of hundreds of engineers lie between my initial design and an AWE kite industry. That said, because this concept even has the slim potential to seriously help the renewable energy sector, I continue to work on it.
So, keeping in mind that I doubt to ever see this play out, an inverting kite farm would look magnificently strange. Dots in the sky—the kites flying thousands of feet high—would slowly ascend, then quickly fall as if dropped, only to slowly rise again moments later. The kites would likely be unsynchronized, so any given moment a handful of scattered dots might be plummeting downwards while dozens more lazily float up. The tethers would be even more unnatural; ropes would seemingly descend from the sky as if some godly puppet master were playing with an earthen marionette. And to drive home the illusion of these kites being other-worldly, you might feel only the slightest breeze on the ground compared to the intense winds at the kites’ level. To a passing observer, they would seem to float.
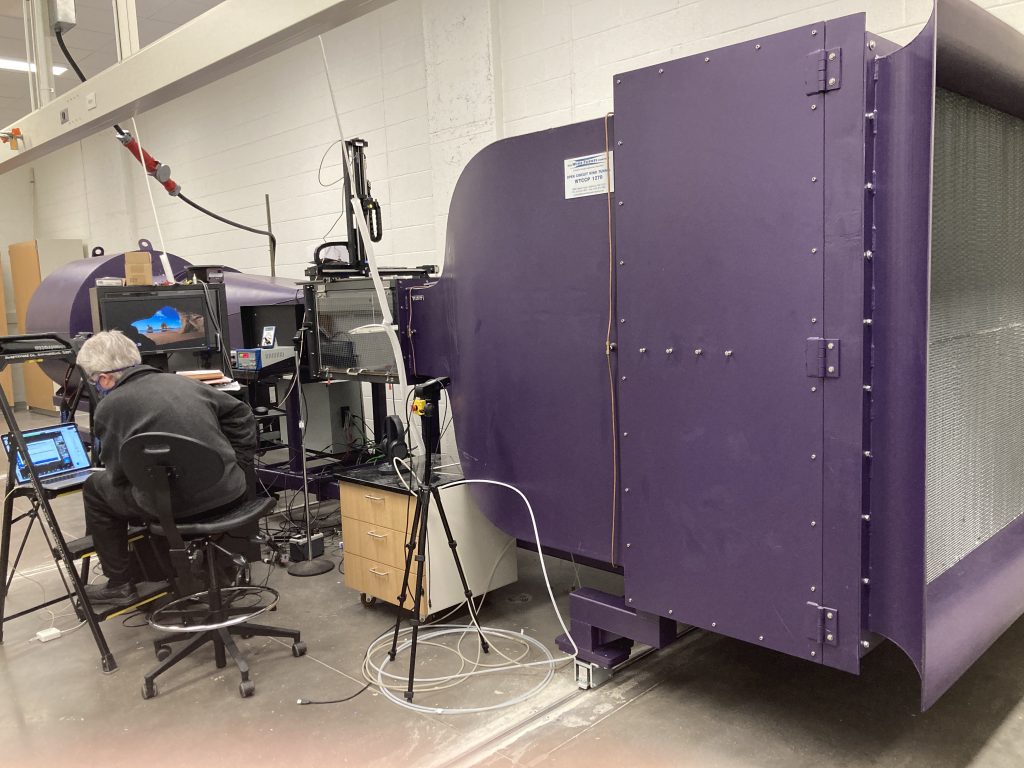
9. How has the Makerspace helped to advance your summer research?
Rapid prototyping is a must for any physical research project, and the Makerspace offered a multitude of 3D printers to accommodate my needs. For an entire week, I 3D printed two new airfoils every day while assembling the two from the day before; I could not have finished my projection time with a single printer alone. Better yet, Jacquie and the Makerspace techs would often replace PLA plastic spools whenever my prints consumed the previous batch. The Makerspace didn’t advance my summer research; it made it possible.