or: How a Mill Becomes a Saw
Good material commands a premium: taking wood from its natural form to something workable in a shop can take an enormous amount of equipment, energy, and time.
Good thing the Makerspace is all about resourcefulness and Swarthmore is packed with intrepid resource hunters! A few years ago, several factors came together to provide us with a unique and wonderful material stream, and many people came together to make happen. Fast-forward to today, where we are slicing some boards from trees that grew right here on campus.
Step one – the logs:
Campus is dotted with large, native hardwood trees that occasionally come down. Several ITS, Makerspace, and Facilities staff intercepted several of these large Oaks and Cypress and slabbed them with the help of a chainsaw mill belonging to ITS’s homegrown lumberjack Andrew Ruether . This mill is a gnarly device that uses a chainsaw like a saw mill and cuts the tree into, in this case, about 2-inch slabs.
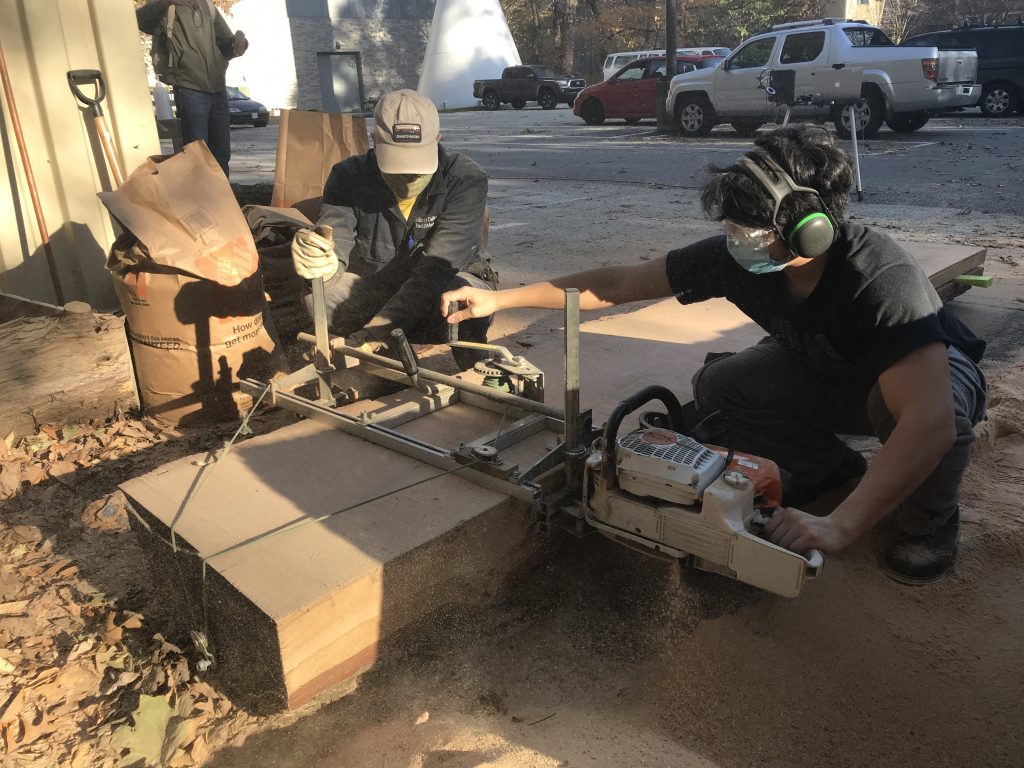
Step two – curing:
Logs don’t like to be put away wet. Differential pressures and internal tensions from moisture leaving the material tends to bend, twist, and rip the wood clear apart. To facilitate slow and steady drying to keep the slabs flat, students and staff built a solar kiln. This is an outdoor ventilated box that uses the gain from sunlight to keep warm, dry air circulating around the stacked slabs… in this case for years.
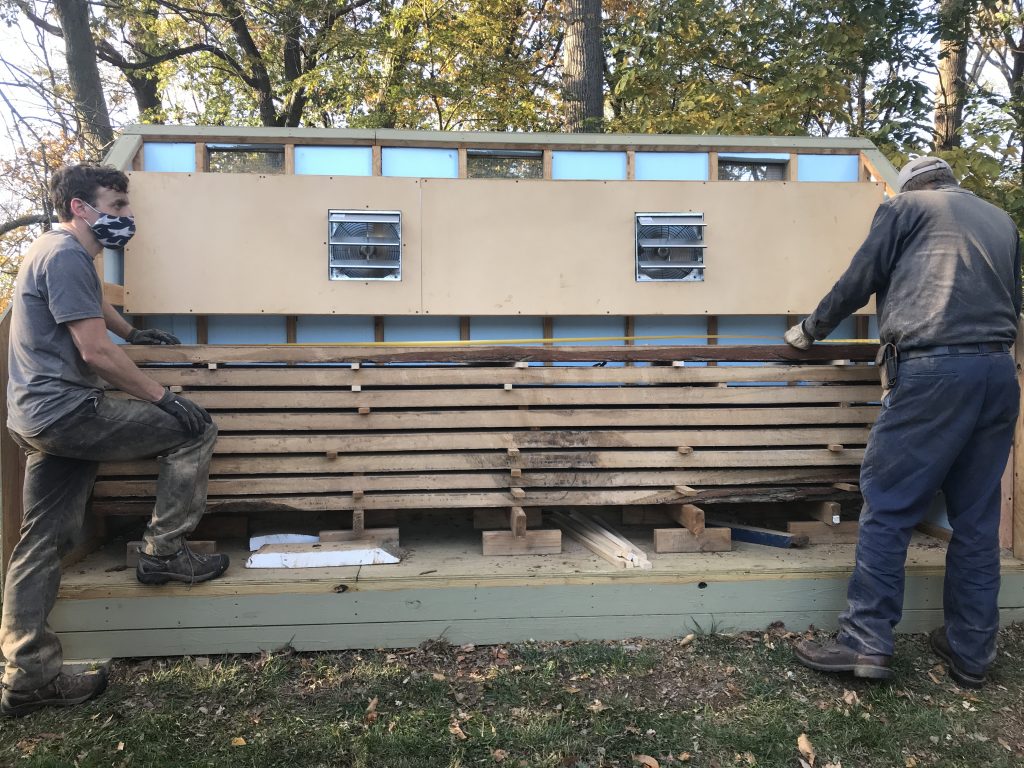
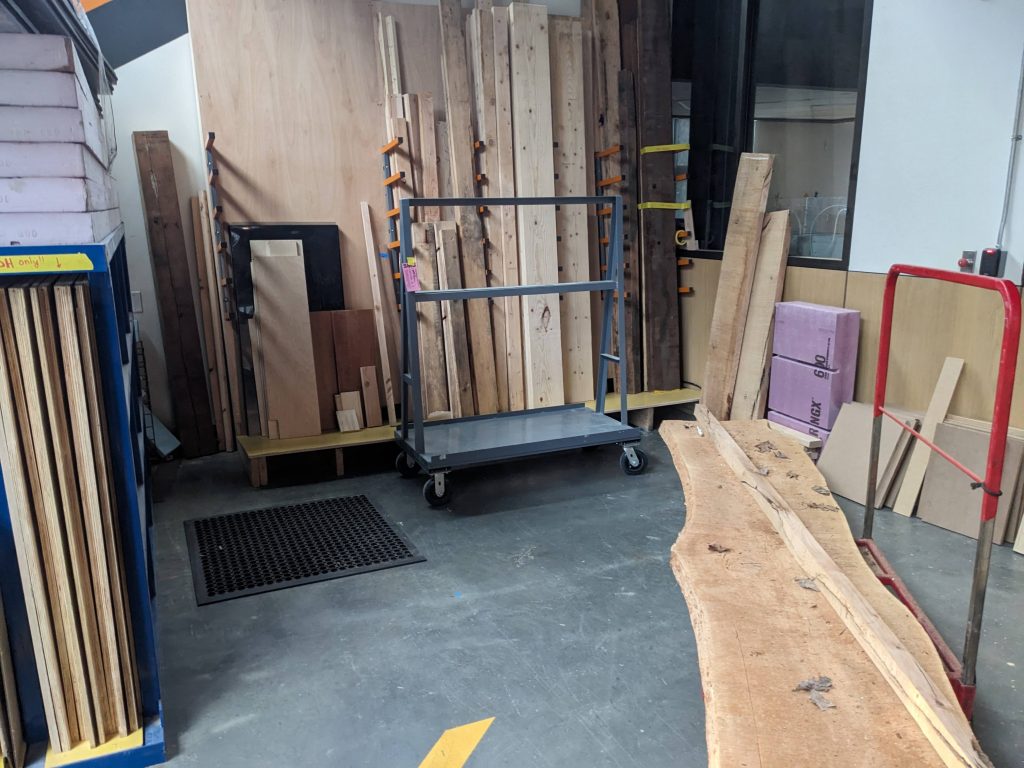
Step 3 – planing and squaring
After the wood cures in the kiln, it’s never quite ready for working. Using large pieces of lumber on conventional woodshop tools requires at least one side of a piece of material to be substantially flat (or something like it). Flattening something this size is a challenge in many shops, and our Makerspace recently deployed the final piece of equipment in the puzzle: our CNC machine!
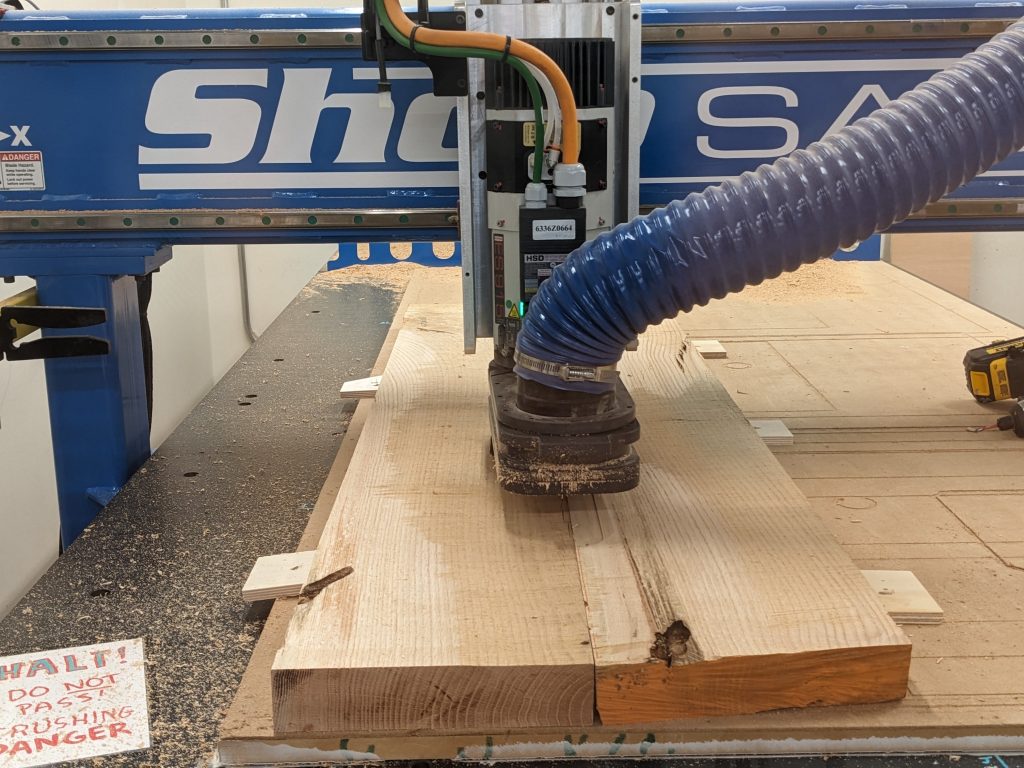
After using a circular saw to rough-cut the slabs into rectangular boards, our CNC machine acts like a 48-inch-wide planing device that renders one side of the boards or slabs completely level.
Finally, these boards get a run through the table saw and/or jointer to get the edges very flat and very close to 90 degrees from each other.
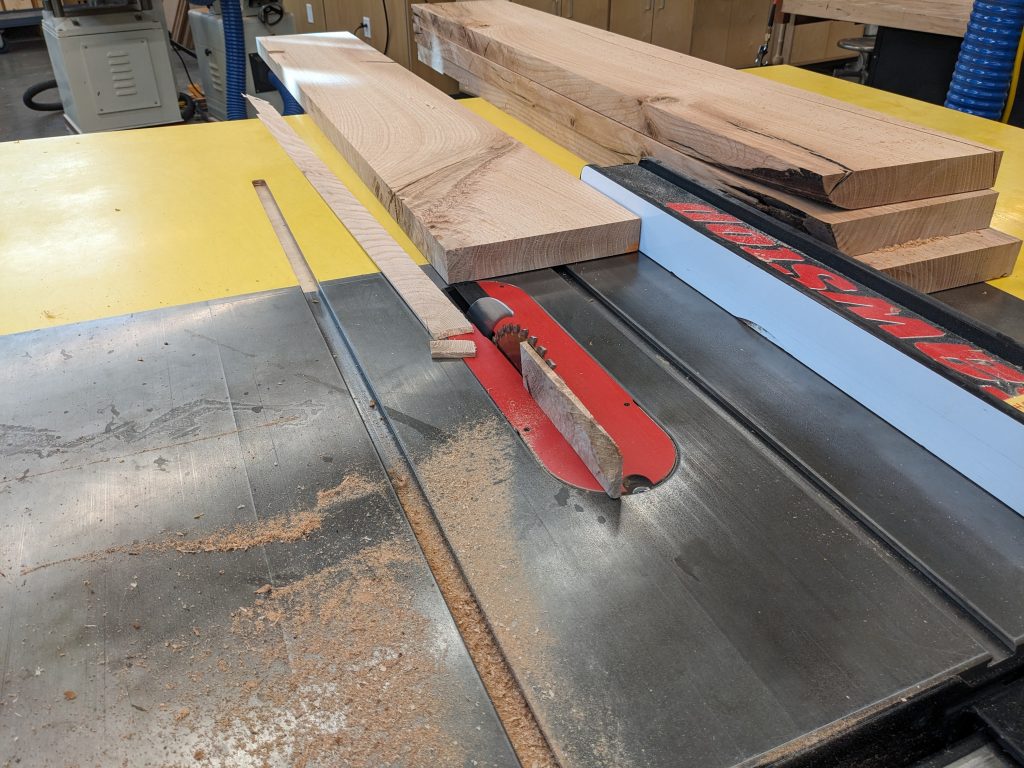
And that’s how a local tree becomes a board! Drop by the Makerspace and let us know what you think we (or you) should make with them!